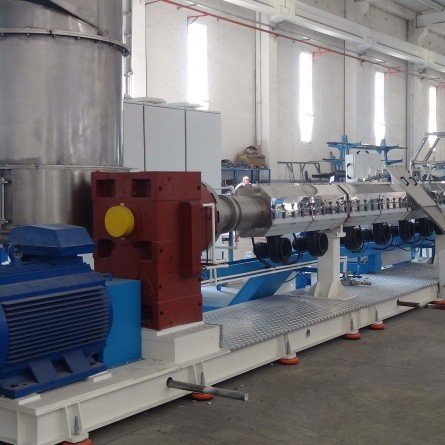
KAPASİTE | 2500-3000 kg. |
IPGC0300-xx | 300 kg/h |
IPGC0500-xx | 500 kg/h |
IPGC0750-xx | 750 kg/h |
IPGC1000-xx | 1000 kg/h |
Recycling of plastics produced for many sectors should be a target for every country that aims to protect the environment and nature as well as our country. For these targets, you can also contribute to nature by using the extruder granule cutting system in your recycling lines. For system information, you can contact our customer representatives via our web address and phone numbers.
As İnan Plastic, our first goal has been to be a trusted and referenced brand with the machines we produce in Turkey and abroad. We respect the environment and resources with the extruder cutting system suitable for recycling all kinds of plastic materials.
Our systems consist of IPGC0300-xx, IPGC0500-xx, IPGC0750-xx, IPGC1000-xx models. Their capacities are 300 kg/h, 500 kg/h, 750 kg/h and 1000 kg/h, respectively. The extruder cutting system is an important stage for plastic recycling.
The machines used in extrusion are similar to the injection machine. A motor turns the screw in a barrel surrounded by heaters, causing the plastic granules under pressure and temperature to melt. In the next stage, the melted plastic flows through the mold and enters into the liquid in the form of a long channel to cool. When it cools, it solidifies and takes form.
The shape of the channel is determined by the shape of the mold. Marking and cutting can be done on the channel. The forms that will come out of extrusion can be square-section, T-section, L-section, U-section, I-section, and a circular section.
The granulation process takes place towards the end of the recycling line. The granule machine should have a powerful vacuum pump and have a comprehensive sieving system. Parts that are not properly washed can cause trouble, therefore the sieve system is important. The ratio between the length and diameter of the screw varies according to the type of material to be processed.
The products formed in the extruder granule cutting system produced by our company are marked, cut, and packaged by the granule cutting system. Thanks to this system machine, several machines have come together. You can contact our customer representatives for detailed information and brochures.
Generally, there are two types of extruders. The more commonly used one is the single screw extruder. Although the twin-screw extruder is not as common as the single screw extruder, it is used in certain sectors. While the single screw extruder operates as a pump, the twin-screw extruder operates like a mixer. Single screw extruder is not a good mixer, but they are highly efficient machines with low maintenance costs.
As İnan Plastic, we mostly recommend single screw extruders in recycling systems.
The main groups that make up the extruders are motor, carrier body, reducer, and barrel. Apart from these main groups, many different subgroups can exist in these machines. The reducer is the part of the extruder that does not accept any errors. Depending on the manufacturer, they have a working life of 30,000 to 50,000 hours.
As İnan Plastic, we are confident in supplying spare parts of all groups, as well as the machine, it is also important to supply parts with certain service life. Their maintenance must be done periodically by an expert team.
Quality, first-class materials are used in the chassis manufacturing of all the machines used in the system.We have models with different capacities from 300 kg to 1000 kg.
Special steel material is used in the production of screws used in the system. Thanks to the special steel used, the screw life is long, which leads to efficiency in the business and less work loss. The outer surface is completely covered with polished bimetal material to extend the screw life. (Bimetal element is formed through the fusing of two metals with different thermal expansion coefficients)
Heat treatment is performed in screw manufacturing and the screw is brought to the hardness degree of 58-63 HRC. We use a water ring, underwater, head, or pasta type pallet cutters in our systems. You can choose our top or side feeding silo models according to the material type.
All screw and barrel materials are meticulously selected against wear. We always protect our customers in terms of material and delivery time in the supply of spare parts. With the models IPGC0300-xx, IPGC0500-xx, IPGC0750-xx, IPGC1000-xx that we manufacture, you can make plastic recycling much more efficiently and quickly. For more technical information, you can obtain detailed brochures from our company.